回路を埋め込んだ3Dプリントを一発出し——エレクトロニクス3Dプリンター「FPM-Trinity」を見てきた
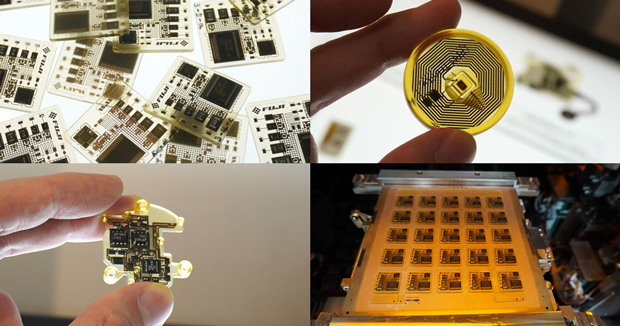
夏に別件の取材で東京ビッグサイトの展示会を訪れた時、あるサンプル展示が目に留まった。3Dプリンターで出力されたと思われる半透明の造形物の中に、電子回路が埋め込まれている。それはちょうど虫の入った琥珀のような見た目だった。そして驚くべきことに、それは1台の装置で、一発で出力されたのだという。そんな夢のような装置、ありえる!?
それから半年が経った今回、ついにその装置を取材することができた。夢の装置、本当にありました。疑って誠に申し訳ございませんでした!!
出力サンプルがやっぱりすごい
伺ったのは愛知県知立(ちりゅう)市にある、FUJI(以下、FUJI)。
エントランスを入ってすぐのショールームにはたくさんの装置がデモ展示されており、その一角に今回紹介するエレクトロニクス3Dプリンター「FPM-Trinity(エフピーエム・トリニティ)」の出力サンプルも置かれていた。
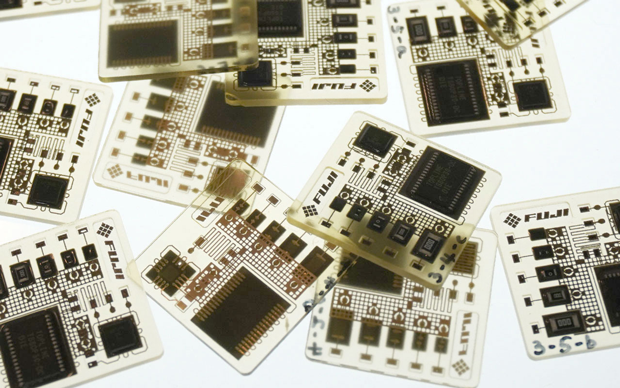
レジンで出力された樹脂板の上に銀ナノインクによる配線が施され、その上に表面実装部品が実装されている。ここまでなら一般的なプリント基板と比べて単なる素材違いという感じだが……。
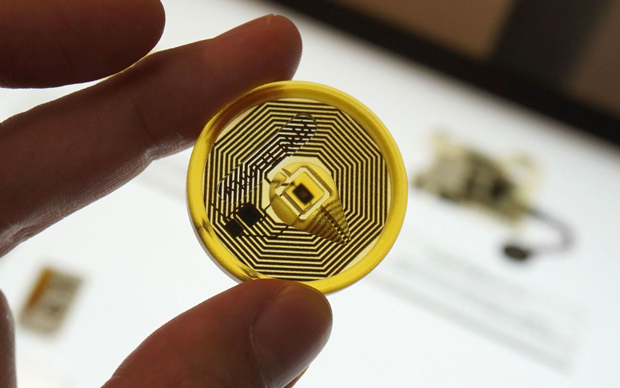
こちらのサンプルは部品実装面の上にも樹脂の層があり、回路が完全にレジンに封入されている。先ほど「虫の入った琥珀」と表現した意味が分かってもらえたと思う。
また3Dプリンターらしく表面に滴型の装飾が成形されているのも見えるだろう。こういった細工も可能なようだ。さらに銀ナノインクの印刷をうまく使ってアンテナが実装されているところにも注目したい。
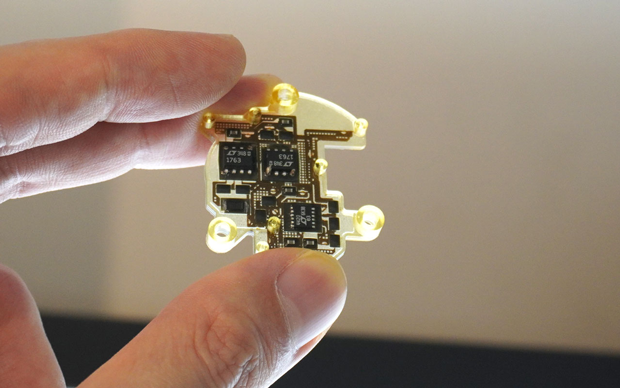
3Dプリントの強みとして、普通のプリント基板にはできない形状の基板が作れる点が挙げられる。輪郭の形状や穴だけでなく、高さ方向の凹凸も可能だ。別途ケースや固定具を作る必要がなく、このまま製品に組み込みやすくなる。
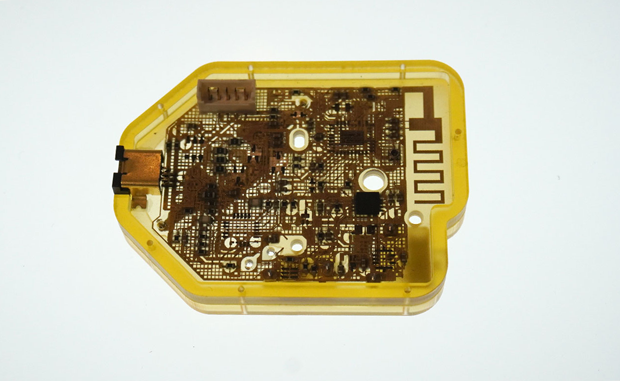
3Dプリントの最大サイズには上限があるが(120×120mm)、回路が大きくなる場合は縦に積んでいくことで広げられる。写真のサンプル基板は4層積み重ねたものだ。
チップマウンターから生まれた、エレクトロニクス3Dプリンター
これらを出力できるFPM-Trinity、一体どんな装置なのか。まだ開発中だという機体を見せていただいた。
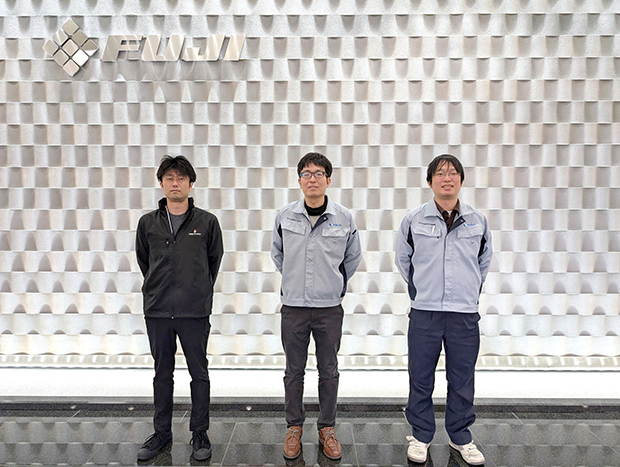
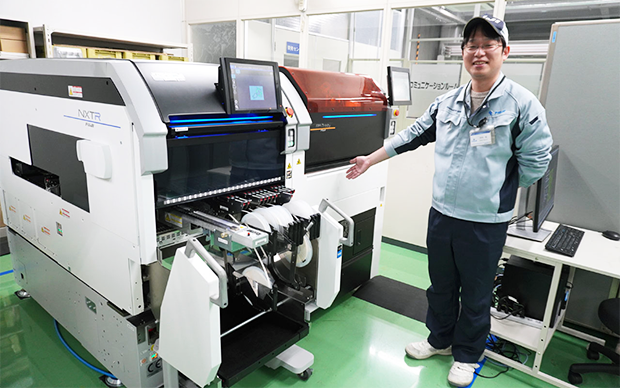
ぱっと見で気づくのが、手前半分と奥半分の2つの装置が連なった構成だろう。
というのも、今回取材したFUJIは、チップマウンター(プリント基板に部品を実装する装置)の大手メーカー。FPM-Trinityの手前半分は、同社のチップマウンターをほとんどそのまま使用しているという。それに3Dプリントやインクジェット印刷等を行う奥半分を連結することで、1台で樹脂成型と回路形成、そして部品実装の一括製造を可能にしている。
その出力工程については下記の資料を見てほしい。
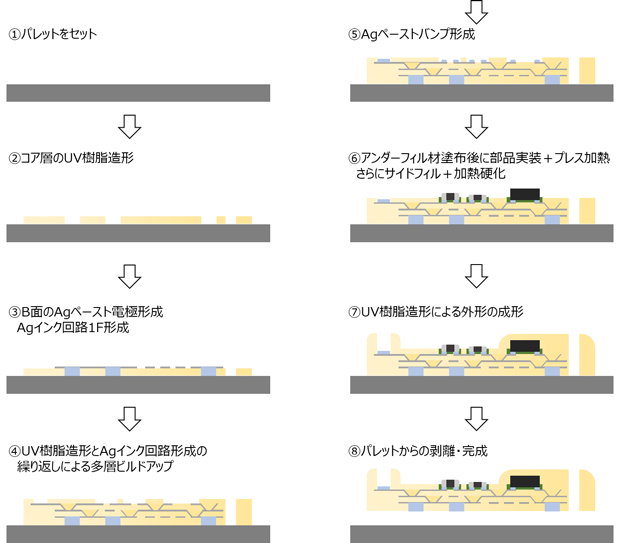
ざっくり説明すると、こんな感じ。
- インクジェット式3Dプリンターで樹脂を成形
- 銀ナノインクのインクジェット印刷で配線を印刷
- 1~2を必要に応じて繰り返し
- 基板のパッド部分に、部品を接着するための銀ペーストを塗布
- マウンターで部品を装着、熱硬化で接合、接着剤で補強
- 必要に応じてさらに樹脂を成形
この工程を全自動で、120×120mmの二層基板なら約1日で行えるという。すごい。
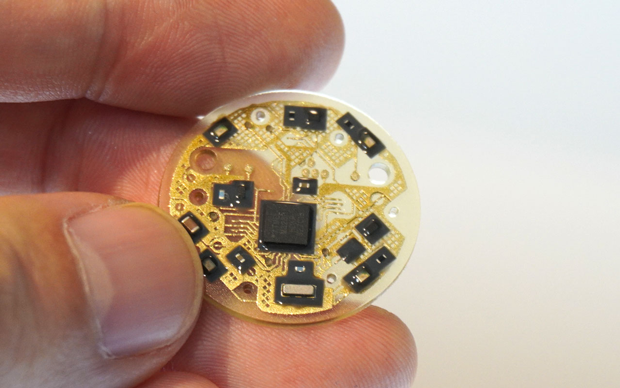
「3Dプリンターで回路まで出力したい」という発想自体は別に突飛ではないものの、これを見るまで僕は「いやそこまでは無理か!」と夢物語の技術だと考えていた。それを実現まで導いたのは、FUJIが15年近く前から取り組んできた研究だ。
開発のきっかけについて、プロジェクトリーダーの富永さんは語る。
「電導インクでの配線や、有機トランジスタの技術が世に出てきた時に、『チップマウンターの役割が印刷に取って代わられるかもしれない』と危機感を抱いたんです。そこで2010年ごろから、将来に向けて印刷で回路を作る技術を研究し始めました。次第にそれがプロトタイプ制作や研究開発用途に向いていることが分かり、製品化を目指すようになりました」
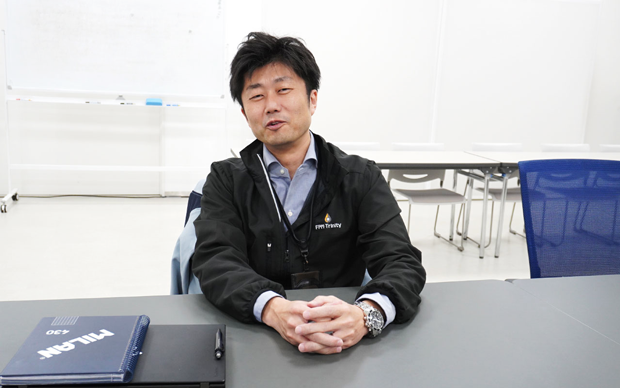
僕はこのエレクトロニクス3Dプリンターについて「造形用の3Dプリンターに回路出力機能が付いたもの」と捉えていた。しかしそれは主従が逆で、実際は回路の印刷から始まっていたのだ。
従来のプリント基板と比べてのメリットは山ほどあるが、まず挙げられるのはプリント基板の外注と比べて完成までが圧倒的に速いこと。そして、少量多品種の製作が可能で、形状の自由度が高いこと。それにより、試作や研究用の基板を少量だけ作るのに最適である。さらに全工程が組織内で完結することで、研究段階の製品のデータが外部に流出しないというメリットもある。
開発に携わる竹内さんはこう語る。
「設計者が製造者にもなれるところが、FPM-Trinityの良さだと思います。自分が設計をしたものが目の前で形になりますし、場合によってはプログラムも自分で書けば1人で製造を完結させることもできます。エンジニアが『作る喜び』を感じられる装置だと感じています」
分かる。めちゃめちゃ分かってしまった。fabcrossでは企業だけでなく個人のものづくりの情報も多く扱っているが、彼らは一様にして「作る喜び」に突き動かされている。
組織が大規模になって分業が進むと、こういった感覚は得られにくい場合もあるだろう。しかしFPM-Trinityが広範囲の工程をカバーすることで1人の技術者ができることも広がり、企業で働くエンジニアにも「自分が作った!」というプリミティブな感動を思い出させてくれるのではないだろうか。
事例紹介:イヤリングからキリンまで
FUJIは将来的にFPM-Trinity装置自体の販売を目指している。現在はその前段階として、製品のブラッシュアップと活用事例の収集を兼ねて、エレクトロニクス3Dプリンターを使った試作サービスを提供している。その中から面白い事例を2つ紹介してもらったので、ここでお見せしよう。
まずはイヤリング。
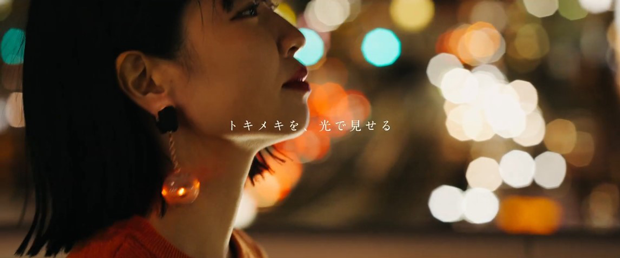
e-lamp.が販売する、心拍と連動して光るイヤリング「e-lamp.」。この試作にFPM-Trinityが使用された。
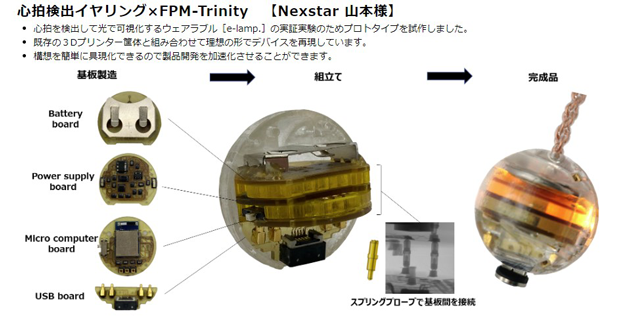
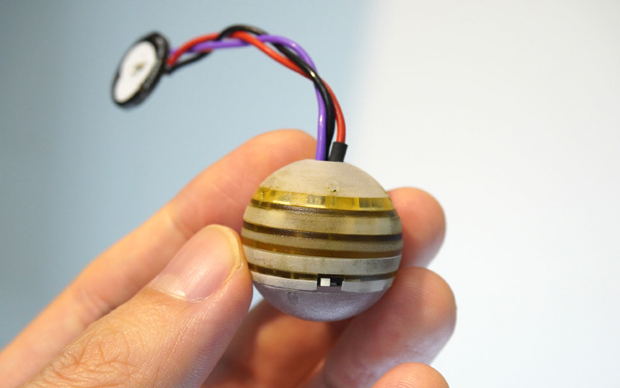
球体の中に、4枚の基板が内蔵されている。これ全体がエレクトロニクス3Dプリンターでの一発出しというわけではないが、一般の樹脂3Dプリンターで作った部品と、FPM-Trinityで出力した部品を組み立てることによって、球体の形状に仕上げている。階層の異なる基板を柱のような部品(資料中の「スプリングプローブ」)で接続している点もユニークだ。
またユニークといえば、九州大学と大牟田市動物園の共同研究に協力した事例もある。跛行というキリンが歩けなくなる病気を事前予知する研究のため、センサーデバイスを製作した。
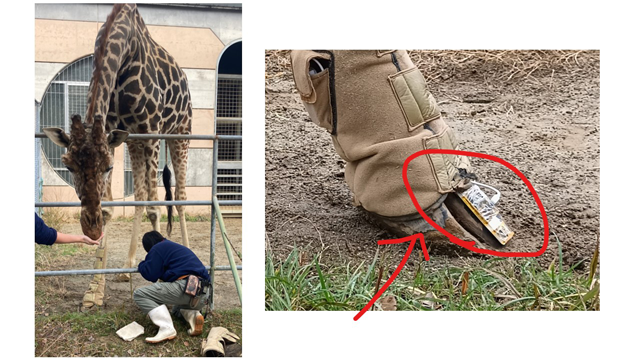

加速度センサーや温度センサー、そしてその値を送信するための無線通信モジュールなどをまとめた基板だ。写真を見ると大きく3つの基板に分かれているが、注目してほしいのはそのつなぎ目の部分。ここはフレキシブル基板ではなく、レジンを薄く出力することで柔軟性を持たせている。
さらに別の事例もある。電動義手用のセンサーの製作評価実績では、人の肌に直接基板を固定する必要があるものの、通常のプリント基板だと形状や凹凸の影響で肌が真っ赤になってしまうという問題があった。FPM-Trinityであれば基板表面の部品に凹凸がなく、フラットかつなめらかな形状で出力できるため、肌への負担をなくすことができたそうだ。
試作サービスを担当している瀧川さんは、次のように話す。
「試作サービスではこれまで、さまざまな用途で50件以上の出力をしてきました。他にも、エレクトロニクス3Dプリンターという装置が今後ものづくりを変えるのではないかということで、装置自体の評価のために出力の依頼をいただくこともあります」
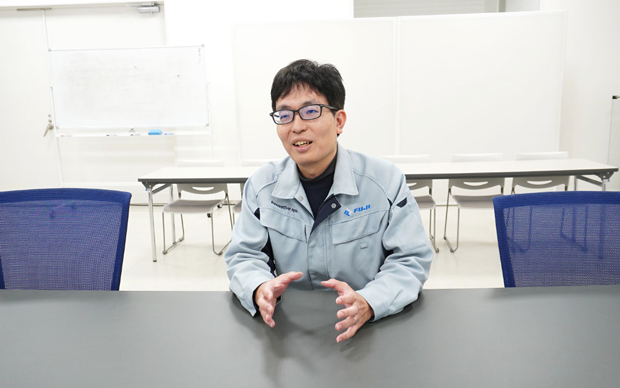
もちろん向き不向きはあって、プリント基板と比べると大量生産向きではないし、出力物の耐久性も劣る。また、工程の都合上サポート材が使用できないため、造形力も単体の3Dプリンターには及ばない。とはいえ、製品化に向けて改善できる点はこれからどんどん改善していくそうだ。
また、近年注目されている環境負荷低減の面でもメリットがある。一般的なプリント基板と比べて、出力時に発生する廃液/廃材が90~95%ほど削減できるほか、3Dプリンターであるためマスク版の製作にかかる資源も削減できるのだそうだ。
FPM-Trinityのこれから
このように、現在は試作サービスを行いつつ、製品としてのブラッシュアップを続けているFPM-Trinity。製品化に向けた作り込みの段階にまで来ているとのことで、プロジェクトも、いよいよ大詰めだ。
とはいえこれだけの装置である。価格帯も基本的には企業向けの製品だ。そこでfabcross的に気になるのは、個人のMakerが触れる機会はあるだろうか、という点。富永さんはこう語る。
「我々も皆さんが身近に感じていただけるよう、積極的に進めたいと思っています。ただ弊社が直接個人向けのサービスをやるのも難しいですから、個人向け製造受託サービスの企業に導入していただくなどして、いろいろな方に使っていただけるとありがたいですね。また公設の試験研究機関やベンチャーインキュベーションラボなどにもぜひ導入していただき、多くの方に使ってもらいたいです」
いやもう本当にこれは、ぜひ実現してほしい。
出力に使用するデータ形式は、一般的なプリント基板に使用するのと同じガーバーデータと、3DモデルのSTLデータがあれば出力可能だそうだ。そう言われると急に身近に思えてきた。
いつか自分が触れる機会が来ることを願って、どんな基板を作るか今のうちに考えておきたい。……というのは嘘で、もう決めてある。ジュラ紀の蚊を模した回路、それ一択である。
